客户背景
福特公司(Ford),是世界第二大汽车制造商(2008年丰田超过通用成为最大的汽车制造商)。1903年由亨利·福特先生创立创办于美国底特律市。现在的福特汽车公司是世界上超级跨国公司,总部设在美国密执安州迪尔伯恩市。1908年福特汽车公司生产出世界上第一辆属于普通百姓的汽车-T型车,世界汽车工业革命就此开始。1913年,福特汽车公司又开发出了世界上第一条流水线,这一创举使T型车一共达到了1,500万辆,缔造了一个至今仍未被打破的世界记录。
今天福特汽车仍然是世界一流的汽车企业,仍然坚守着亨利.福特先生开创的企业理念: “消费者是我们工作的中心所在。我们在工作中必须时刻想着我们的消费者,提供比竞争对手更好的产品和服务。” 福特汽车公司旗下拥有的汽车品牌有阿斯顿·马丁(Aston Martin)、福特(Ford)、捷豹(Jaguar)、路虎(Land Rover)、林肯(Lincoln)、马自达(Mazda)和水星(Mercury)。
客户面临的挑战
项目目标是对标本田,借助FTI系统设计出更优化的白车身零件,降低零件复杂度,提高材料利用率
•制定达标系统,经理层设定材料利用率目标
•依托FTI系统建立成本自动分析系统
•建立多样化的零件成本分析、优化模板
•建立持续改进的工作模式
•定义标准化的优化设计建议,实现零件设计的快速 “优化--分析--验证”闭环
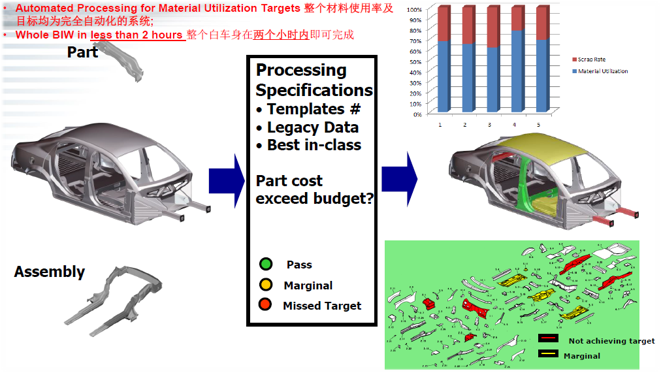
FTI 解决方案
提升材料利用率,降低单件成本
建立规范化的工作流,在产品开发流程中使用FTI系统分节点对零件的成型性、材料利用率进行分析,通过预设置的优化策略对原设计进行快速优化、迭代,提升材料利用率,降低成本。
减少设计更改、缩短研发周期
通过FTI成本分析-优化系统,促进零件设计师与工艺工程师之间的紧密互动,从设计源头开始关注零件的材料利用率并显著提升零件的可制造性,避免后期工艺问题和设计更改,缩短开发周期。
零件成本精确可控,提升议价空间
从设计的早期阶段即可对零件的材料成本、制造成本有较准确的把控,并能随着设计更改进行快速的自动更新;模板化的成本分析报表在与供应商的议价中能为柳汽提供准确、可靠的依据,赢得议价空间。
强化设计工艺协同,提升研发实力
依托系统建立“设计—工艺”协同、并行开发的高效模式,在柳汽设计和工艺部们形成良好的人人关注成本、优化成本的精益设计、制造习惯,实现“面向制造的设计”目标,提升自主研发实力。
客户价值
“By FTI tools, we increased MUD, reduced material costs ($ 500M USD), and have noticed part complexity decrease...”
“通过FTI工具,我们提高了材料使用率,降低了材料成本(约5亿美金),同时也实现了零件复杂程度的降低…”
——James Morgans
VP Process Engineering, Ford Motor, 2013
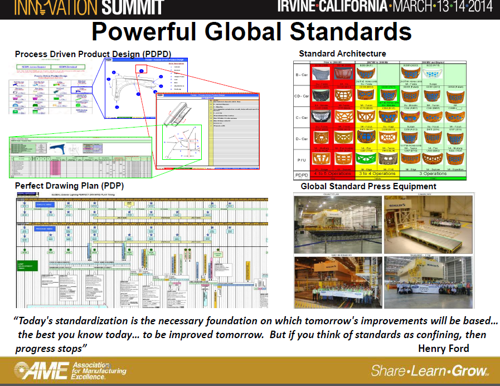
•为白车身设计、制造部门建立了一套从贯穿管理层到零件设计师的零件成本分析、优化系统,财务部门也通过系统进行多项目预算估算、成本比较分析
•使设计到工艺的每个环节都建立起对材料利用率的关注,在开发过程中主动使用分析工具进行材料利用率和成本分析,优化设计
•通过系统与供应商协商改进材料利用率、单件成本,使外协件的成本议价更规范、准确、透明