CAE助力企业降低模具开发成本——JSTAMP导入事例介绍之一
发布时间:2020-7-14发布人:admin
1) 试模时发现开裂与回弹→反复修模→项目进度延时; 2) 团队成员流动大,研发经验无法积累与传承; 3) 新增CAE软件的投入产出比(ROI),是否能够为公司带来真实效益等。 |
面临这样的共性问题,有没有可行的办法来解决?
通过调研国内外大型汽车制造商及其零部件加工企业的实际应用发现,使用 CAE 工具是解决上述问题的有效解决办法。CAE(Computer Aided Engineering)是计算机辅助工程的简称,在工程设计中利用计算机辅助求解分析与优化复杂工程和产品的结构力学性能等,把工程或生产中的各个环节有机地组织起来,将有关的信息集成,使其产生并存在于工程或产品的整个生命周期。具体到冲压行业,即在试模前,使用 CAE 工具同步辅助研发冲压零部件及其加工数模,用计算机硬件加专业的冲压仿真成形软件结合数字化的设计方案来代替实际的冲压设备及模具进行虚拟试模,提前预测并解决在后续实际试模时可能出现的缺陷,例如常见的起皱、开裂与回弹问题,进而缩短试模时间,节省成本。
使用 CAE 工具同步辅助研发冲压零部件的典型流程 一、 广州某日系汽车部件有限公司导入JSTAMP软件的过程 1. JSTAMP 软件导入前公司现状(2006~2012年) 1).零件使用材料等级最高为590Mpa 2).2010年前,模具研发由日本母公司支援,使用母公司出货前设计的数模,试模时成形性与精度都没问题,模具的修模次数平均为1次 3).2011年后,由于该公司增加了专门针对中国车型的零件,从而日本母公司支援困难,因此,面临的主要问题是第一次试模时常常出现成形性不合格与回弹量过大,靠人工经验及试错法修模,修模次数平均为7次,进而导致零件制作周期延长,即为没有导入CAE工具之前大家面临的共性问题。
2. JSTAMP 软件导入后公司产品研发情况(2013~2020年)
1).零件使用材料等级从780Mpa,逐渐升级最高为1180Mpa
2).利用 JSTAMP 软件,独立推进高强钢模具研发能力的积累与建立,目前具备超高强钢零件(材料等级1180Mpa以上)的研发能力
3).通过使用 JSTAMP 软件辅助模具研发,对零件的成形过程进行仿真分析可以在试模前提前验证成形性并消除成形性问题,通过回弹精算及其自动补偿技术的应用提高零件的回弹控制精度,实现修模次数由原来未使用仿真时平均7次降低到现在的平均3次以内,进而缩短零件制作周期
3. JSTAMP 软件辅助该公司产品研发的应用实例
1).试模时消除起皱与开裂成形性问题
2).提高了零件回弹控制的初始精度,进而修模平均次数在3次以内即可满足零件的精度要求
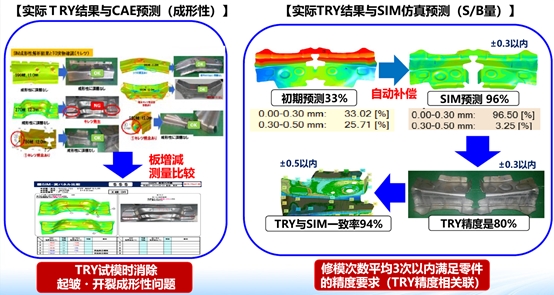
二、 广州某日系汽车部件有限公司导入JSTAMP软件后带来的实际效益
具体到开篇对我们所关注的三个问题,导入 JSTAMP 软件后带来实际效益的答案如下。
1).试模时消除起皱与开裂成形性问题,提高了零件回弹控制的初始精度,进而修模平均次数在3次以内即可满足零件的精度要求,因此,可以大幅度提升项目研发进度
2).该公司的技术顾问反馈,使用JSTAMP 提供的功能建立企业内部仿真案例库与仿真项目设定模板,并制定相应的仿真技术应用的操作规范来积累并传承企业内部技术经验,对公司年轻工程师的培养有莫大的帮助
3).根据收集的数据初步估算公司投入产出比大于10
导入CAE 解决方案的费用为Z=JSTAMP软件+硬件
每套模具每次修模的成本计算:X=人工费用+耗材(电费、材料费、设备损耗等)
通过导入JSTAMP 软件每套模具平均减少了修模次数为4次,4*X
假设公司年制作模具数量Y套,则每年为公司节省成本为 4*X*Y
由此计算投入产出比为:Z/4*X*Y > 10(通过该公司导入JSTAMP前后的数据统计估算)